The Essential Guide to Mold Injection Plastic in the World of Metal Fabricators
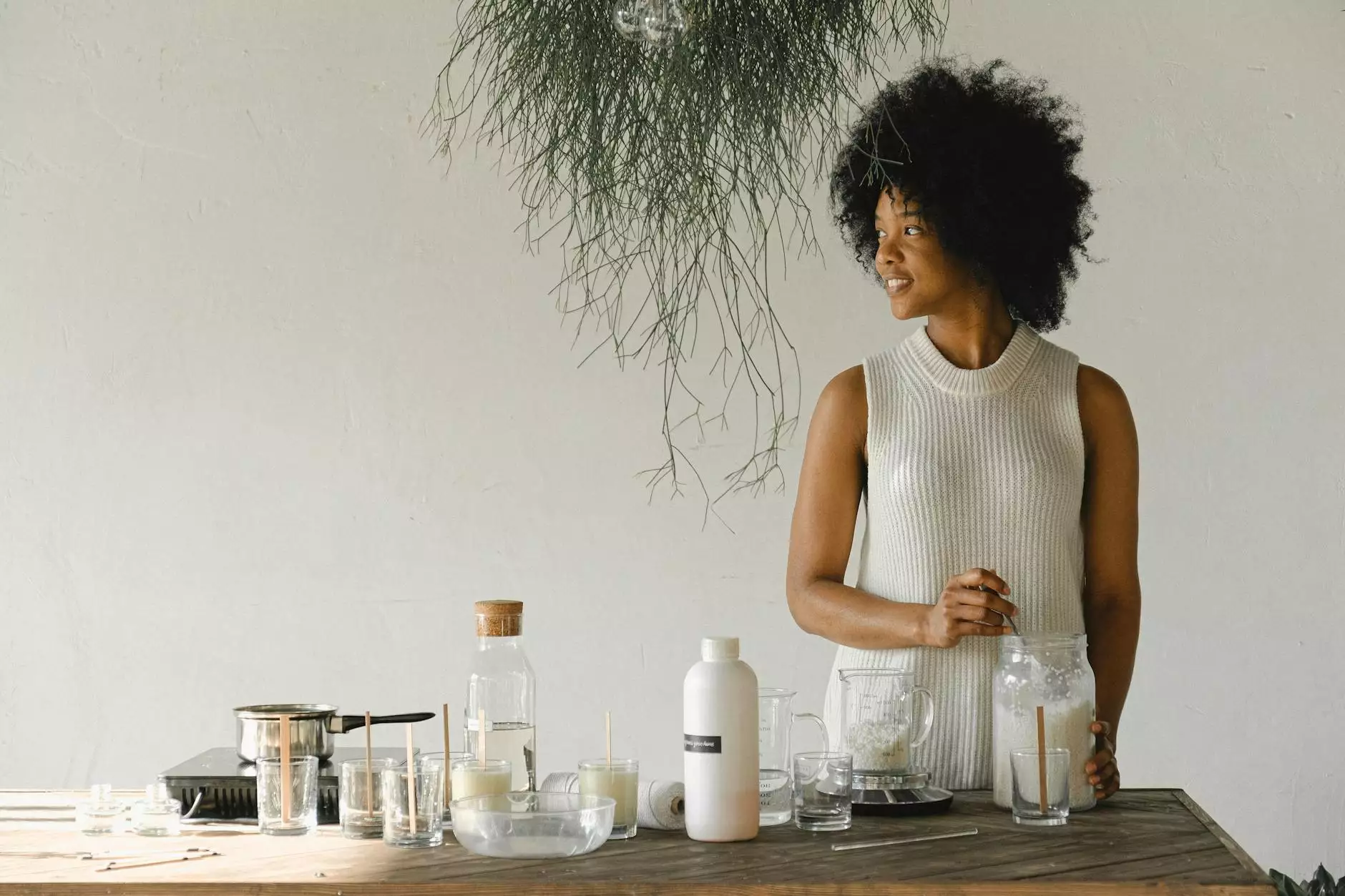
Understanding Mold Injection Plastic
Mold injection plastic is a highly efficient and versatile manufacturing process that allows businesses, particularly in the metal fabrication industry, to produce precise and consistent parts at scale.
This method involves forcing molten plastic material into a mold cavity, where it cools and solidifies into the desired shape. The capabilities of mold injection plastic are immense, allowing for complex designs, reduced waste, and rapid production times, making it a preferred choice for manufacturers like DeepMould.
Reasons to Choose Mold Injection Plastic
The appeal of mold injection plastic lies in its numerous benefits, which include:
- High Efficiency: Once the mold is designed and created, mass production can begin, with cycle times often as low as a few seconds.
- Consistency and Precision: Each part produced is identical, minimizing the need for post-production adjustments.
- Material Versatility: A wide variety of plastic materials can be used, catering to different needs and applications.
- Reduced Waste: The process is designed to use only the necessary amount of plastic, significantly cutting down on excess material.
- Complex Geometries: Intricate designs that might be impossible with other processes can be easily achieved with meticulous molding.
The Mold Injection Process Explained
The mold injection plastic process consists of several key steps:
- Designing the Mold: A custom mold is designed using CAD software, ensuring it meets the exact specifications required for the final product.
- Creating the Mold: High-quality materials such as steel or aluminum are used to manufacture the mold, providing durability and precision.
- Melting the Plastic: Plastic pellets are heated until melted, transforming them into a liquid suitable for injection.
- Injecting the Plastic: The melted plastic is injected into the mold under high pressure, ensuring it fills all cavities evenly.
- Cooling and Solidifying: After injection, the plastic cools and solidifies in the mold, taking on its final shape.
- Removing the Part: Once cooled, the mold is opened, and the newly formed part is ejected.
- Finishing Touches: Additional processes like trimming, painting, or assembly may follow to prepare the part for use.
Applications of Mold Injection Plastic in Metal Fabrication
In the realm of metal fabricators, mold injection plastic finds its application in numerous sectors, including:
- Automotive Industry: Used for producing dashboard components, light housings, and various interior parts.
- Consumer Electronics: Essential in creating casings for phones, tablets, and other devices.
- Medical Devices: Offers precision for intricate devices where accuracy is critical.
- Household Products: Used in making containers, furniture, and a variety of everyday items.
- Aerospace Components: Lightweight parts that reduce weight without sacrificing strength.
Mold Injection Plastic Innovations at DeepMould
DeepMould is at the forefront of adopting innovative techniques in the mold injection plastic industry. Some of the advancements include:
- Advanced Material Use: Incorporating environmentally friendly materials that comply with stringent regulations while maintaining performance.
- Automation: Utilizing automated machinery to enhance production speed and reduce human error.
- Smart Monitoring Systems: Implementing IoT technology to monitor the production process in real time, ensuring quality control.
- 3D Printing Integration: Combining traditional molding with 3D printing for rapid prototyping and design verification.
- Data Analytics: Using data-driven decisions to optimize maintenance schedules, decrease downtime, and improve overall efficiency.
Challenges in Mold Injection Plastic
While mold injection plastic offers numerous advantages, there are challenges to be aware of:
- High Initial Costs: The expense involved in designing and creating molds can be prohibitively high for small-scale operations.
- Limited Material Choices: Not every type of plastic is suitable for injection molding; selecting the right material is crucial.
- Design Constraints: The complexity of the mold's design can limit the intricacy of the parts produced.
- Cycle Time Optimization: While fast, the molding process can be slowed down by inefficient cooling and heating methods.
The Future of Mold Injection Plastic
The future of mold injection plastic looks promising, driven by several emerging trends:
- Sustainability: The industry is moving towards greener practices with biodegradable plastics and energy-efficient processes.
- Customization: As demand for unique products increases, the ability to customize molds for limited runs will become more significant.
- Technological Advancements: Continued integration of artificial intelligence and machine learning in the manufacturing process will enhance efficiency and reduce costs.
- Integration with Other Technologies: Merging traditional methods with modern techniques such as additive manufacturing will broaden applications.
Conclusion
In conclusion, mold injection plastic stands as a testament to modern manufacturing, offering unparalleled efficiency and versatility. For metal fabricators looking to elevate their production capabilities, adopting this technology is not merely an option but a strategic necessity. With innovative companies like DeepMould leading the charge, the potential for growth and advancement in this sector is limitless.
As the industry evolves, staying informed about advancements and best practices in mold injection plastic will ensure that businesses remain competitive in an ever-changing market landscape. Embrace the future of manufacturing with confidence.