Die Casting and Injection Moulding: A Comprehensive Guide for Metal Fabricators
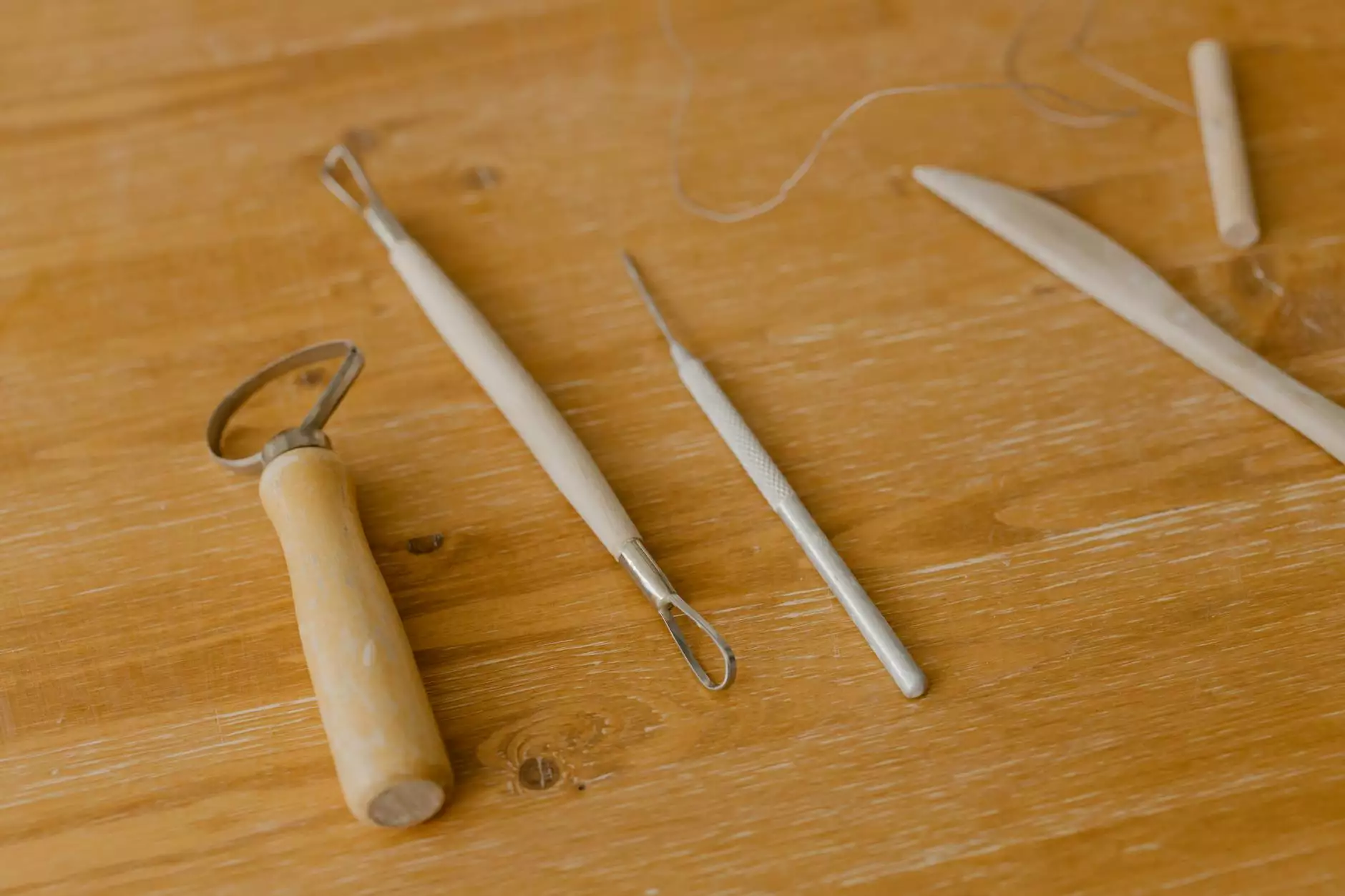
In the realm of metal fabrication, two prominent techniques continue to gain traction due to their efficiency and versatility—die casting and injection moulding. These methods not only streamline the manufacturing process but also enhance the quality and precision of the components produced. This article will explore the intricacies of die casting and injection moulding, their applications, advantages, and how they shape the future of the manufacturing industry.
What is Die Casting?
Die casting is a metal casting process that involves forcing molten metal under high pressure into a mould cavity. This technique is renowned for producing parts with intricate details and high dimensional accuracy. Primarily used for non-ferrous metals like aluminum, zinc, and magnesium, die casting is invaluable in industries such as automotive, aerospace, and electronics.
How Die Casting Works
The die casting process can be broken down into several steps:
- Preparation: The metal is melted in a furnace to reach the desired viscosity.
- Injection: The molten metal is injected into a steel mould under high pressure.
- Cooling: The metal cools and solidifies rapidly within the mould.
- Extraction: Once cooled, the part is ejected from the mould.
- Finishing: Additional finishing processes such as machining, polishing, or coating may be applied.
Advantages of Die Casting
Die casting offers several significant benefits, particularly for metal fabricators:
- High Precision: Die casting enables the production of highly accurate parts with minimal finishing required.
- Complex Geometries: This method allows for the creation of intricate shapes that would be challenging to manufacture through traditional methods.
- Cost-Effectiveness: Once the mould is created, the cost per part decreases significantly, making it ideal for high-volume production.
- Superior Surface Finish: Parts produced by die casting exhibit excellent surface finishes, reducing the need for secondary operations.
Understanding Injection Moulding
Injection moulding is a manufacturing process for producing parts by injecting molten material into a mould. While more commonly associated with plastics, injection moulding is also applicable to metal components, particularly when dealing with metal powders or metals that can be processed as a slurry. This method is prevalent in producing durable and precise products across multiple industries.
How Injection Moulding Works
The steps involved in injection moulding are as follows:
- Material Preparation: The raw material, typically a plastic or metal powder, is heated until melted.
- Injection: The molten material is injected into a closed mould under high pressure.
- Cooling: The material cools and solidifies in the mould, taking its shape.
- Ejection: The finished part is ejected from the mould.
- Post-Processing: Additional steps such as trimming or painting may be completed after ejection.
Advantages of Injection Moulding
Injection moulding boasts several advantages that make it a popular choice in metal fabrication:
- Efficiency: This process allows for rapid production cycles, making it suitable for large-scale manufacturing.
- Design Flexibility: It enables the production of intricate designs and complex features with ease.
- Low Waste: The nature of injection moulding minimizes waste materials, making it an environmentally friendly option.
- Consistency: Offers high levels of repeatability and consistency in the quality of parts produced.
Comparing Die Casting and Injection Moulding
While die casting and injection moulding share similarities, they differ significantly in applications, materials, and process characteristics:
FeatureDie CastingInjection MouldingMaterialPrimarily non-ferrous metalsPlastics and some metal powdersProduction VolumeHigh-volume productionIdeal for both low and high volumesComplexityHigh complexity and thin walls possibleGreat for complex shapes and materialsDimensional AccuracyHighVery HighInitial Setup CostHigherLower to moderateApplications of Die Casting and Injection Moulding
Both die casting and injection moulding cater to a wide array of industries due to their tailored capabilities:
Die Casting Applications
Die casting is extensively used in various sectors:
- Automotive: Engine blocks, transmission cases, and other complex components.
- Aerospace: Structural components that demand lightweight and strong materials.
- Consumer Electronics: Housings and intricate parts for electronic devices.
- Household Appliances: Components that require durability and aesthetic appeal.
Injection Moulding Applications
Injection moulding is favored in numerous industries, including:
- Medical Devices: Safe, precision parts for life-saving equipment and tools.
- Packaging: Containers and lids that need to be produced quickly and consistently.
- Toys: Imaginative designs that require vibrant colors and durability.
- Consumer Goods: Everyday items like utensils, tools, and even furniture components.
The Future of Metal Fabrication with Die Casting and Injection Moulding
As industries continue to evolve, so do die casting and injection moulding technologies. Innovations such as 3D printing integration, smart moulds, and the use of advanced materials are set to revolutionize these processes. The adaptability of both techniques positions them well to meet future manufacturing demands, particularly in producing lightweight parts that enhance fuel efficiency and product performance.
Sustainability in Metal Fabrication
With the growing concern for sustainability, both die casting and injection moulding are adapting by:
- Recycled Materials: Increasing the use of recycled metals and plastics to minimize resource depletion.
- Energy Efficiency: Implementing energy-efficient machinery and practices to reduce carbon footprints.
- Circular Economy: Fostering practices that allow for the recovery and reuse of materials.
Conclusion
In conclusion, die casting and injection moulding play crucial roles in the metal fabrication sector. Their unique processes, advantages, and diverse applications form the backbone of many industries. By staying informed about the latest technologies and practices, businesses like DeepMould can leverage these techniques to improve productivity and meet the growing demands of the market effectively.
For metal fabricators looking to embrace these manufacturing methods, understanding the nuances of die casting and injection moulding will undoubtedly open up new avenues for innovation and growth in today's competitive landscape.