Understanding Die Casting Components: A Comprehensive Guide for Metal Fabricators
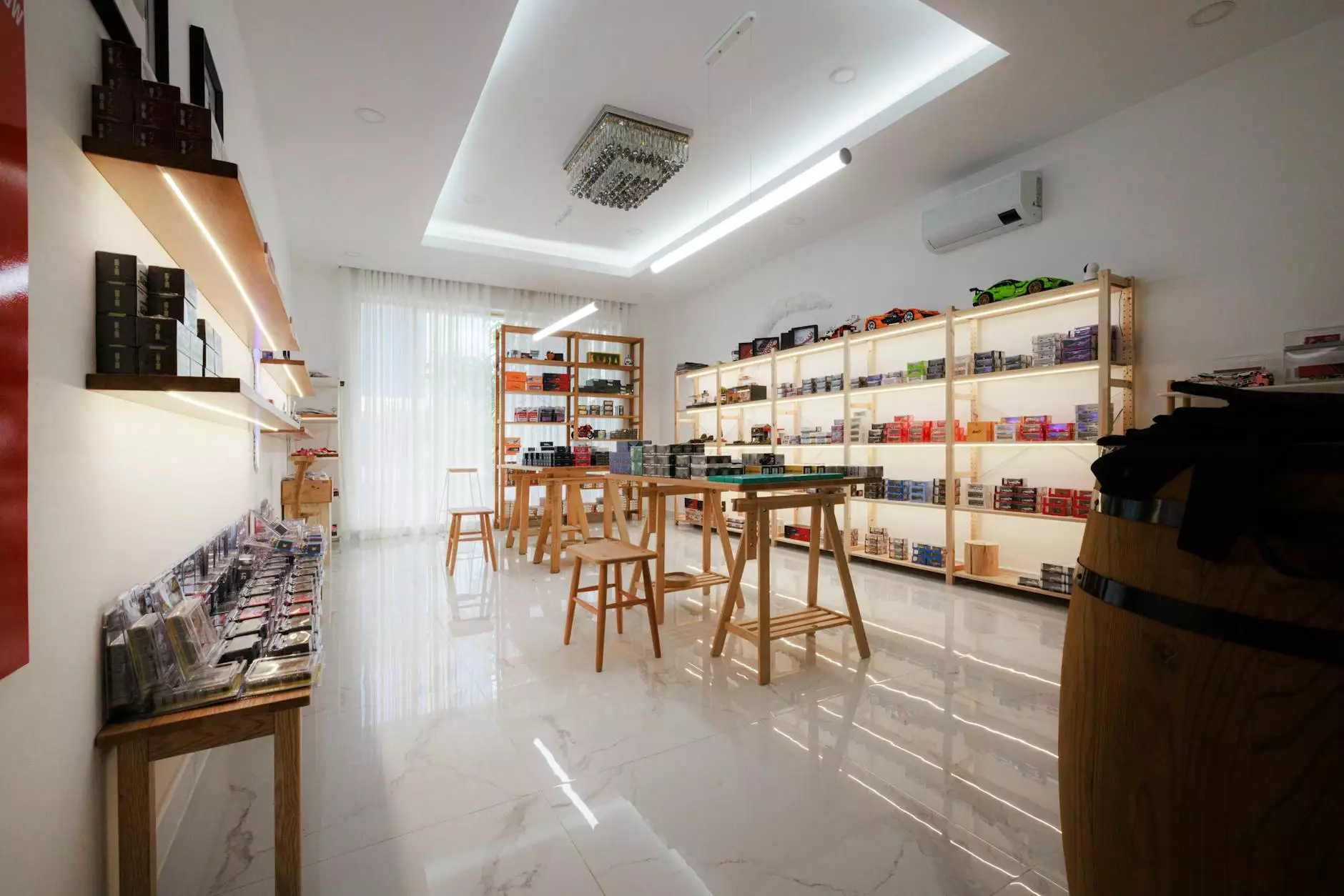
Die casting components are crucial elements in the metal fabrication industry, particularly for manufacturers seeking to create precise, durable, and intricate parts. This article delves deep into the technology, processes, advantages, and applications of die casting components. We will take a closer look at how they contribute to enhancing product quality and manufacturing efficiency.
What are Die Casting Components?
Die casting components are created through a manufacturing process that involves forcing molten metal into a mold cavity under high pressure. This method allows for the production of complex shapes and thin-walled parts with high dimensional accuracy. Die casting is widely used in various industries, including automotive, aerospace, consumer goods, and electronics.
The Die Casting Process
Understanding the process of die casting is essential for appreciating the value of die casting components. The procedure involves several key steps:
1. Preparation of the Die
The die, or mold, is usually made from high-strength steel or iron to withstand the pressure and heat involved. The die is designed with the desired shape of the component and is lubricated for easy release of the finished part.
2. Melting the Metal
Different metals can be used in die casting, including aluminum, zinc, and magnesium. The metal is melted in a furnace until it reaches a molten state, ready for injection.
3. Injection into the Die
Once the metal is molten, it is injected into the die at high speed and pressure. This step is crucial as it ensures that the molten metal fills every part of the mold, forming the intricate details of the component.
4. Cooling and Solidification
After the injection, the molten metal begins to cool and solidify inside the die. The cooling time depends on the metal used and the thickness of the part.
5. Ejection
Once solidified, the die is opened, and the finished die casting components are ejected from the mold. Any excess material, known as flash, may be trimmed away during this stage.
Advantages of Die Casting Components
Choosing die casting components over traditional manufacturing processes comes with numerous benefits:
1. High Precision and Accuracy
Die casting produces parts with excellent dimensional stability and tight tolerances, which is essential for applications requiring a high degree of precision.
2. Complex Geometries
The die casting process allows for the creation of intricate designs that may be impossible with other methods. This capability is particularly beneficial in industries such as automotive and aerospace.
3. Surface Finish
Parts produced by die casting often have superior surface finishes, reducing or eliminating the need for additional machining or finishing processes.
4. Material Efficiency
Die casting minimizes waste since the process produces very little scrap metal. The excess material can often be recycled and reused in future runs, making it an environmentally friendly choice.
5. Cost-Effectiveness
While the initial investment in dies can be high, the long-term savings from reduced manufacturing time and material waste make die casting a cost-effective solution for high-volume production.
Applications of Die Casting Components
Die casting components are utilized across various industries thanks to their unique properties:
- Automotive: Engine parts, transmission cases, and structural components.
- Aerospace: Aircraft components, housings for avionics, and structural elements.
- Consumer Electronics: Housings for laptops, tablets, and smartphones.
- Industrial Equipment: Components for machinery and tools.
Types of Die Casting
There are two primary types of die casting processes commonly employed in manufacturing:
1. Hot Chamber Die Casting
In hot chamber die casting, the casting machine uses a gooseneck to inject molten metal into the die. This method is suitable for alloys with low melting points, such as zinc. However, hot chamber casting is limited to low-melting-point metals.
2. Cold Chamber Die Casting
Cold chamber die casting is used for metals with higher melting points, such as aluminum and magnesium. In this process, the molten metal is poured into a chamber and then injected into the die. This separation of melting and injection allows for greater versatility in material choices.
Choosing the Right Die Casting Partner
When selecting a company for die casting components, consider the following factors to ensure you receive the best quality and service:
1. Expertise and Experience
Choose a partner with a proven track record in die casting and a deep understanding of the specific industry requirements.
2. Quality Assurance Practices
Ensure that the manufacturer employs rigorous quality control measures to maintain high standards in the production process.
3. Range of Services
Look for a provider that offers a comprehensive range of services, including design assistance, prototyping, and post-casting machining.
4. Advanced Technology
Partnering with a company that utilizes state-of-the-art technology and equipment can result in better precision and efficiency.
Future Trends in Die Casting Components
The die casting industry is continually evolving, and several trends are shaping its future:
1. Automation and Industry 4.0
Automation technologies are being integrated into die casting processes, improving efficiency and reducing human error.
2. Sustainable Practices
As environmental concerns grow, many manufacturers are adopting sustainable practices, including recycling and using eco-friendly materials.
3. Advanced Alloys
The development of new alloys that enhance performance while reducing weight is becoming increasingly important, particularly in aerospace and automotive applications.
Conclusion
In conclusion, die casting components play a pivotal role in the metal fabrication industry. Their precision, cost-effectiveness, and versatility make them the preferred choice for many manufacturers. Understanding the die casting process, its advantages, and applications can help businesses leverage this technology to their advantage. As the industry continues to innovate, partnering with a knowledgeable provider like DeepMould can ensure you remain at the forefront of manufacturing excellence.
Contact Us
If you are seeking a reliable partner for your die casting components, look no further than DeepMould. We are dedicated to providing high-quality solutions tailored to your needs.