CNC Machining Parts Service: Revolutionizing Metal Fabrication
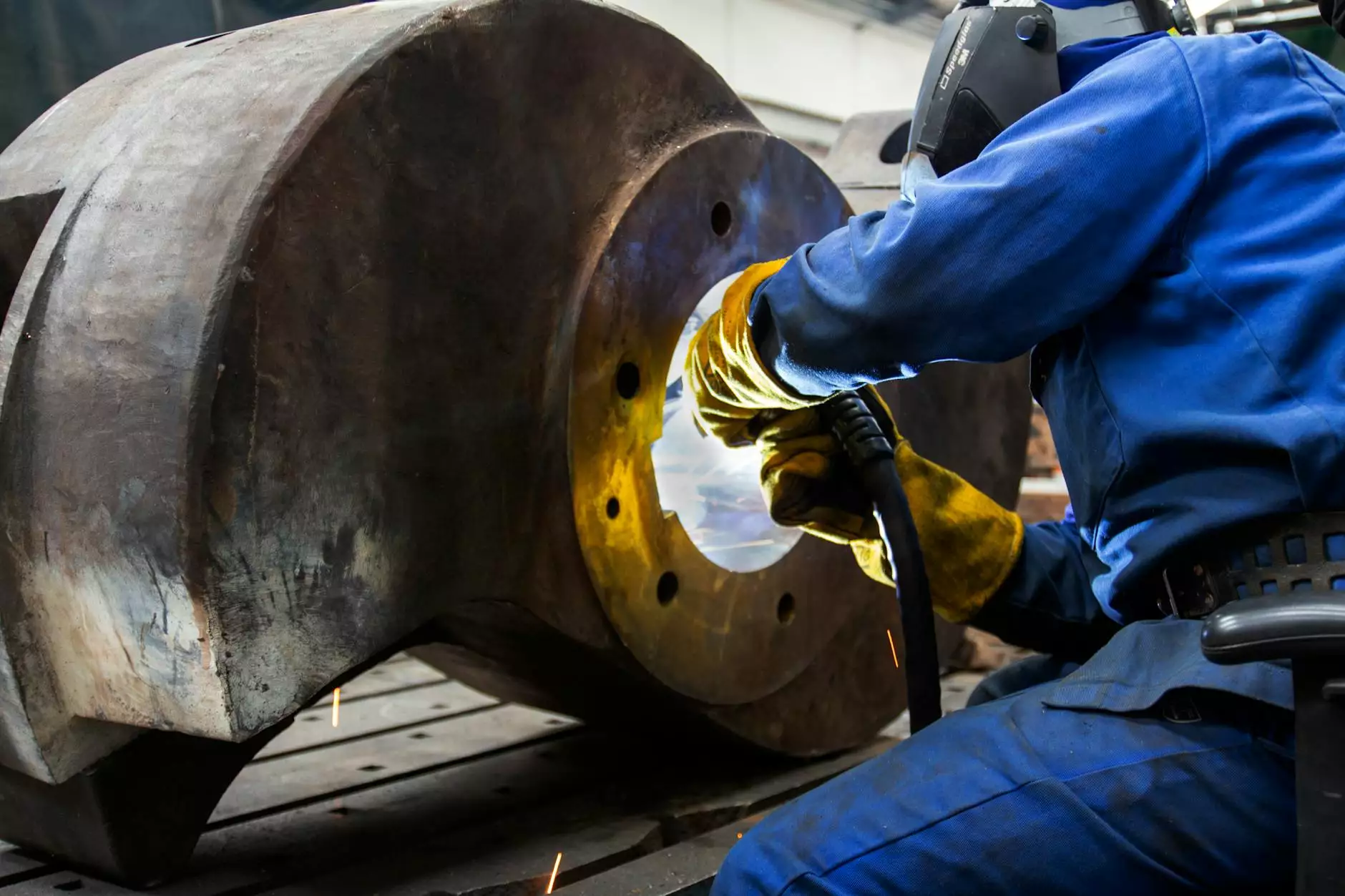
CNC machining parts service has become a cornerstone of modern manufacturing, especially for metal fabricators. By integrating advanced technology with traditional craftsmanship, businesses like Deep Mould are setting new standards for quality, precision, and efficiency. In this article, we will delve into the manifold advantages of CNC machining and explore how it can enhance operations for metal fabricators.
The Importance of CNC Machining in Modern Manufacturing
As industries evolve, the demand for precision and efficiency has never been higher. CNC—Computer Numerical Control—machining automates the manufacturing process, offering unparalleled accuracy. For metal fabricators, this technology signifies a leap forward:
- Enhanced Precision: CNC machines operate using precise calculations from CAD software, ensuring that every cut and shape is executed with remarkable accuracy.
- Consistency: Unlike conventional machining methods, CNC machining guarantees uniformity across batches, significantly reducing the risk of human error.
- Speed: Automation accelerates production times, allowing for rapid prototyping and quicker turnaround on projects.
- Complex Geometries: CNC machining excels at creating intricate designs that would be impossible or exceedingly difficult to achieve manually.
Understanding CNC Machining Parts Service
At its core, cnc machining parts service involves several key processes that metal fabricators must understand in order to take full advantage of the technology:
1. Prototyping and Design Validation
Before full-scale production, fabricators can create prototypes to test and validate designs. This process is crucial for identifying potential issues early, saving both time and resources.
2. Customization
One of the standout features of CNC machining is its ability to easily accommodate custom specifications. Whether it’s a particular dimension, material, or finish, fabrication services can tailor solutions to meet every client’s unique needs.
3. Batch Production
Once a design is validated, CNC machining enables efficient batch production. This is particularly advantageous for metal fabricators who require multiple pieces with consistent quality.
4. Quality Control
Quality is paramount in metal fabrication. CNC machines come equipped with advanced monitoring systems that ensure every part meets stringent quality standards. This built-in quality control minimizes defects and maximizes customer satisfaction.
How CNC Machining Parts Service Benefits Metal Fabricators
The integration of CNC machining into a metal fabrication business model offers several benefits that can significantly impact overall operations:
1. Cost Efficiency
While the initial investment in CNC technology can be considerable, the long-term cost savings are substantial. Factors contributing to this include:
- Reduced Material Waste: Precision machining minimizes scrap materials, leading to significant savings.
- Lower Labor Costs: Automation reduces the need for extensive manual labor, allowing personnel to focus on higher-value tasks.
2. Increased Production Capacity
CNC machining allows for simultaneous operation of multiple machines, vastly increasing production capabilities. This efficiency means that fabricators can take on larger projects and satisfy higher customer demand without sacrificing quality.
3. Improved Worker Safety
By automating dangerous tasks, CNC machining reduces workplace accidents. Operators can oversee machines from a safe distance, minimizing risk while maximizing productivity.
4. Environmental Benefits
CNC machining is more environmentally friendly than traditional methods due to its efficiency. Less energy consumption and reduced waste contribute to a lower carbon footprint, making it a sustainable choice for forward-thinking metal fabricators.
Choosing the Right CNC Machining Parts Service Provider
Finding the right partner for your CNC machining parts service needs is crucial for achieving business success. Here are some factors to consider when making your choice:
1. Expertise and Experience
Look for a provider with extensive experience in the industry. A seasoned company will possess the necessary skills to handle complex projects and overcome potential challenges effectively.
2. Technology and Equipment
Ensure that the service provider utilizes state-of-the-art CNC machines. Advanced technology translates to higher precision and better overall quality in the finished products.
3. Customer Testimonials and Reviews
Feedback from previous clients can provide valuable insight into the provider’s reliability and quality of service.
4. Turnaround Times
In today's fast-paced market, timely delivery is essential. Make sure you inquire about production timelines and the provider's ability to meet your deadlines.
Integrating CNC Machining Into Your Business Strategy
As a metal fabricator, integrating cnc machining parts service into your operations can transform your business. Here are steps to ensure successful integration:
1. Training and Development
Invest in training your workforce on using CNC technology. Skilled operators are critical in maximizing machine capabilities and ensuring quality production.
2. Continuous Improvement
Embrace a culture of continuous improvement. Regularly review processes and outcomes, seeking opportunities to enhance efficiency and quality.
3. Collaboration with Engineers
Establish strong communication between fabricators and engineers to ensure that designs are optimized for CNC machining. Early collaboration can uncover potential issues, leading to better final products.
4. Future-Proofing Your Operations
Stay abreast of emerging technologies in CNC machining. As innovations continue to change manufacturing dynamics, adapting to new developments will keep your business competitive.
Conclusion: The Future of Metal Fabrication with CNC Machining Parts Service
CNC machining parts service is not just a trend; it is reshaping the landscape of metal fabrication. By leveraging modern technology, metal fabricators can achieve higher levels of precision, consistency, and efficiency. Investing in CNC machining processes not only enhances production capabilities but also positions businesses like Deep Mould for long-term success in a competitive marketplace. As the industry evolves, embracing these advancements is key to thriving in today’s fast-paced manufacturing environment.